
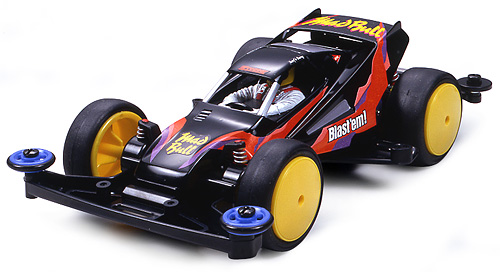
The causes of contact overheating include insufficient capacity, insufficient contact pressure, surface oxidation or dirty, etc. The faults of contact components generally include contact overheating, wear, and welding. This will affect the contact reliability of the relay. The main drawbacks are loose contacts, cracks in the contacts, or excessive size and position deviation. Some products' contacts are press-fitted by riveting. In the e-core of the AC relay, when the air gap of the center column disappears due to the abrasion of the cores on both sides, the armature sticks and cannot be released.Ĭontacts are electrical contact parts used by relays to switch loads. When the sub-magnetic ring on the iron core of the AC relay is broken, or the armature and the pole face of the iron core are rusted or invaded, it will cause the armature to vibrate and generate noise.Ĥ. In some DC relays, due to mechanical wear, or damage to the non-magnetic gasket, the minimum air gap after the armature is closed becomes smaller, and the residual magnetism is too large, resulting in a malfunction that the armature cannot be released.ģ. The edges and corners and the shaft are worn out, causing the armature to turn ineffectively or stuck.Ģ. During maintenance, the air gap can be adjusted to 0.02-0.05mm, or the spring can be replaced.ġ. The break of the short-circuit ring can also cause loud noise.Īfter the power is off, the armature cannot be released immediately, which may be caused by the moving iron core being stuck, the iron core air gap is too small, the performance is poor, and the iron core contact surface is oily. If there is oil stains, it can be cleaned.

The coil can be removed and the contact surface can be filed or polished. The armature is noisy after power-on, which may be caused by uneven contact surfaces of the moving and static iron cores, or oil pollution. If the armature cannot be sucked up after the iron core is energized, it may be caused by the broken wire of the coil, foreign matter between the static iron core, and low power supply voltage. When the AC coil is connected to voltage, the armature of the AC coil may not be closed due to the failure of the transmission mechanism or jamming, which will cause the coil to burn out. Because the coil voltage is connected incorrectly, for example, a coil with a rated voltage of 110v is connected to a 220v power supply voltage, or an AC voltage coil is connected to a DC voltage of the same level and the coil is immediately burned out.ĥ.When the coil voltage exceeds 110% of the rated voltage, the operating frequency is too high, or when the voltage is lower than 85% of the rated voltage, the AC coil may be burned out because the armature fails to pull in.Ħ. During maintenance, the coil insulation may be damaged due to the tool's bruising, or the wire may break.Ĥ.
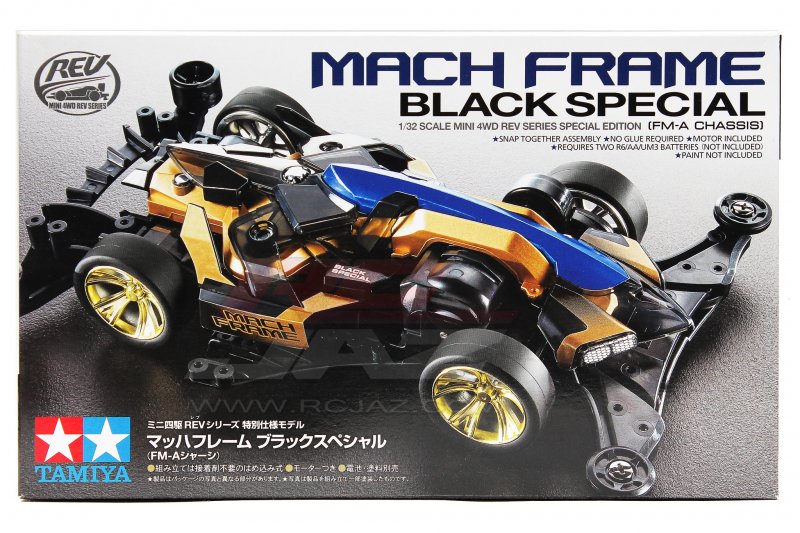
The coil is damaged due to the coil voltage exceeding 110% of the rated voltage.ģ. Due to changes in ambient temperature (exceeding the specified value of the technical conditions), the coil temperature rise exceeds the allowable value and causes damage to the coil insulation the insulation level is severely reduced due to moisture internal disconnection or short circuit between turns due to corrosion.Ģ. Attention should be paid when assembling and welding, otherwise the relay level will be reversed.ġ. For coils that have a start and end requirement, the start and end are generally marked with a marking method. When welding, pay attention to distinguishing, otherwise it will cause the coil welding error. Multi-winding coils are generally made of lead wires with different colors. If the pressure is too small, the winding will loosen and the magnetic loss will increase. When the electromagnetic system is riveted, the pressure adjustment of the hand lever press and the press should be moderate, too much pressure will cause the coil to break or the coil frame to crack, deform, and the winding breakdown.
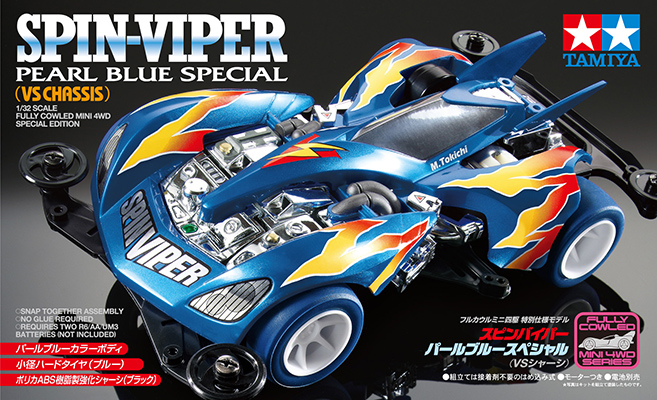
If they collide and are connected, they will break when they are separated. The coils should be separated and placed in special appliances. There are many types of coils used in relays, either outsourced or outsourced. The faults of electromagnetic components are mainly in the coils and moving and static iron cores. ( What are the precautions when using relays?) Relay troubleshooting is usually analyzed from two aspects: electromagnetic components and contact components. During the use of the relay, due to various reasons, such as poor product quality, improper use, poor maintenance, etc., various failures often occur.
